Grand Opening











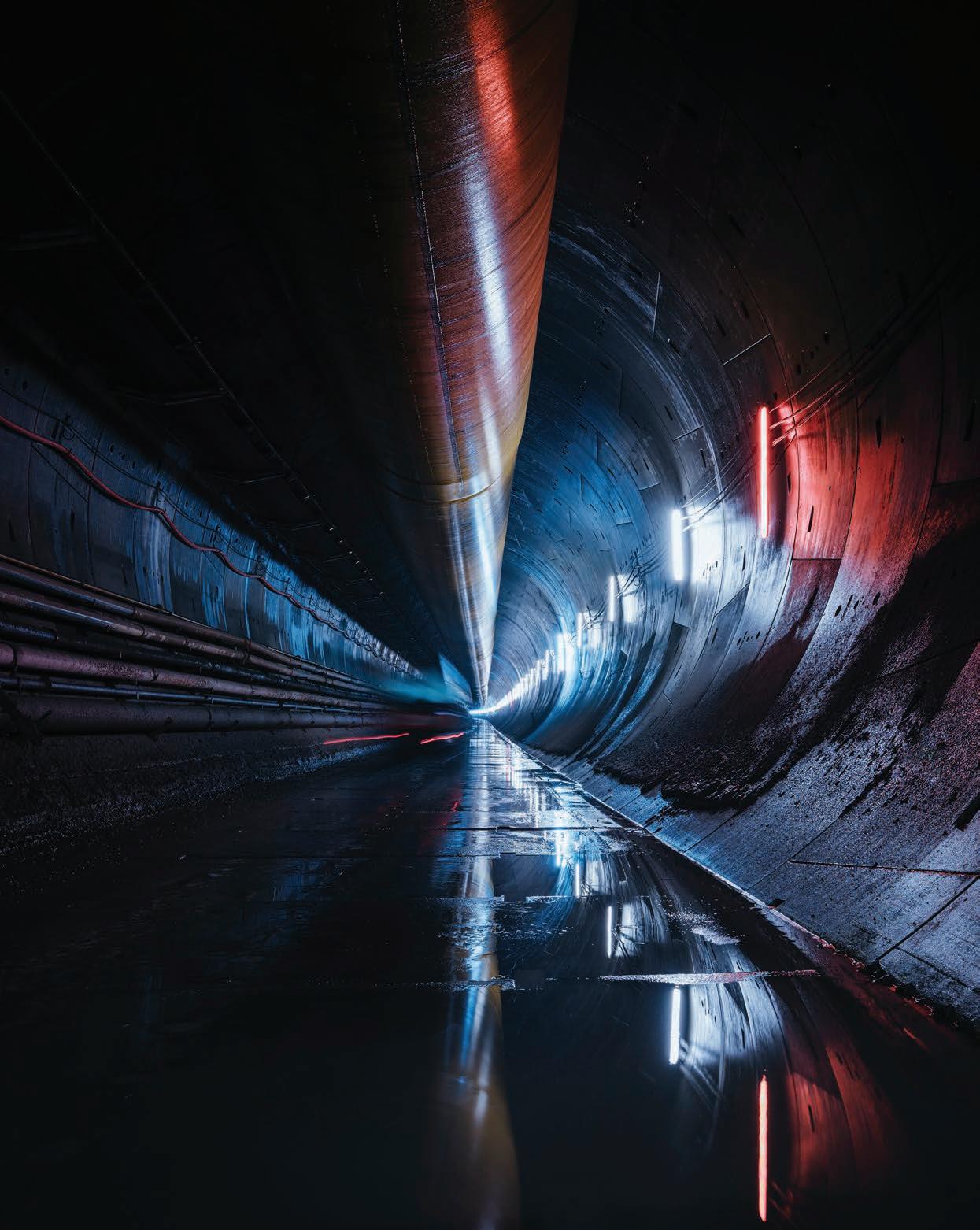
Line

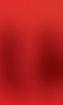










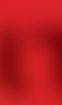

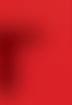

























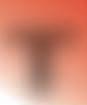
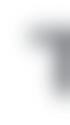



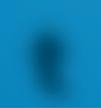











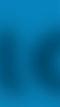

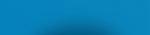



























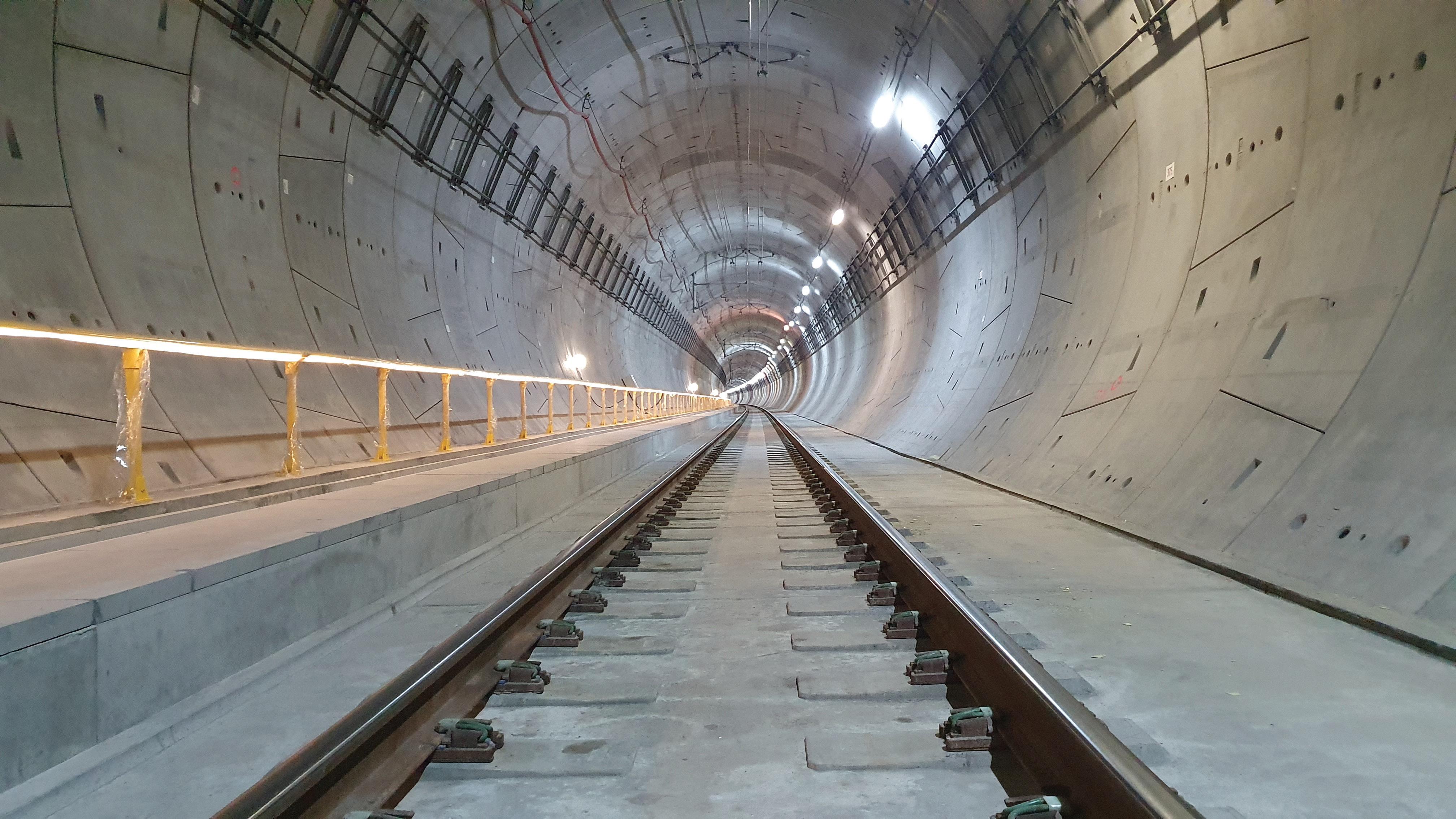


Royal inauguration and public opening of the Follo Line high-speed railway in Norway
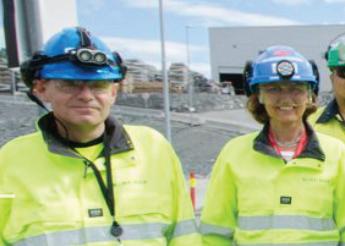

December 2022 TunnelTalk reporting
There was mounting anticipation and excitement for arrival of King Harald V and Crown Prince Haakon of Norway as they joined other dignitaries, guests, and members of the public to celebrate the official opening of the new Follo Line high-speed railway line between Oslo and the town of Ski in Norway in early December. All were gathered to celebrate the major achievement of completing a multi-complex, predominantly underground and dedicated double track section of high-speed modern rail infrastructure within seven years of awarding the first main construction contract.
Completion of the project and its opening to public service is a triumph for international contracting, and for the excavation processes of drill+blast, drill+split and mechanised TBM tunnelling with a precast segmental lining in hard rock. It is also a testament to management and inter-management cooperation between client and contractor and to the resolution of all to get the job done. It has not been without challenges and difficult situations, but all has been achieved and Bane NOR, the Norwegian National Rail Company and client, has earned the right to lead the celebrations under its project leadership of CEO Gorm Frimannslund and Project Director Anne-Kathrine Kalagar.
The foresight of Bane NOR began in the earliest stages of planning when the decision was made to excavate the longest tunnel on the project, the 20km long, twin-tube Blix tunnel, with four TBMs, and to line the tubes with bolted and gasketed precast segments. Drill+blast and drill+split near sensitive urban infrastructure would play an important role on the shorter complex approach tunnels near Oslo and for
excavation of the access adits, assembly chambers and 44 cross passages on the Blix tunnel, as well as for the cut-andcover platforms at Oslo Central Station, but selection of TBMs for the majority of the underground alignment was contrary to national and international expectations for the project in hard Norwegian rock. As well as speed of excavation and onepass rail tunnel construction, together with reduced designlife maintenance costs, the TBM option was supported by other environmental and social commitments made by the client to those impacted by the project:
• There would be no intermediate access points on the 20km long twin tube Blix tunnel
• All excavation by the four TBMs would advance from a single access jobsite and rig area provided by the client and located in the middle of the alignment
Table 1. Follo Line project statistics
22km of new double track railway from Norway´s capital city to the new public transport centre in Ski
Comprise the construction of about 64km of new railway tracks including 20km in twin running tunnels (40km in total) and realignment of tracks underground for the existing Østfold Line on the approach to Oslo Central Station and to the new Ski Station

Forms the core part of InterCity development southwards from Oslo Is Norway’s longest railway tunnel to date and the longest rail tunnel in the Nordic countries
Excavated mainly with four TBMs (40km) as well as 1.5km of drill+blast and drill+split in urban and sensitive areas
Enables a 50% reduction in journey time between Oslo and Ski – from 22 to 11mins – at 250km/hr train speeds
Main construction started in 2015
Public rail services began in early December 2022
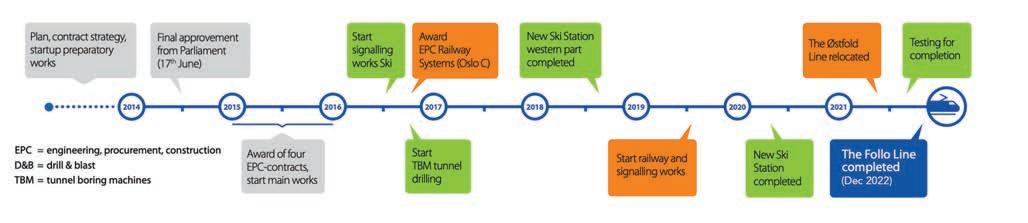
Seven years and 18 million working hours spent in construction works by more than 2,000 companies and contractors with Bane NOR as client, more than half being Norwegian or Norwegian registered companies with a significant contingent of international participators
Gas detection system
12 bar water pressure resistance in static mode
Number of grouting ports
Number of drilling rigs
Non-flammable conveyor belts
Refuge chambers in compliance with ITA guidelines - 24hr stand-up time
• There would be no lowering of the groundwater table either during construction or in railway operation, and
• To maintain high speeds, as the start of highspeed rail connections to neighbouring Sweden and Europe beyond, there would be no intermediate stops between Oslo and Ski.
The next foresight by the client was to base the construction contracts on the EPC (engineering procurement construction) model and to open competition for the contracts to the international market. The EPC form of contract is particularly favoured in Scandinavia and is, for all intents and purposes, a turnkey contract with the contractor responsible for design, procurement, construction, commissioning, and handover of the fully completed infrastructure project. By opening an international procurement process, all parties interested in the contracts were invited to submit prequalification statements and shortlisted bidders were invited to bid the work. Prequalification and joint venture groups included contractors and associated design engineers from the world over including Turkey, Korea, Austria, Germany, France, Italy, Spain, as well as Norway, Sweden and Denmark. With an international procurement process established, the client, as a government authority, also stipulated that the wages and conditions of
employment for workers on the project would comply with Norwegian national labour regulations and standards.
At its peak, workers on the project came from more than 62 different countries of the world from as far afield as Colombia, the Philippines, China, South Africa, and most countries of Europe.
Next, the client purposefully inserted itself with its consultant experts, directly into the design and procurement strategy of the TBMs to be used on the long Blix tunnel. With the likelihood of an international group being awarded the long twin tube TBM project, the client knew best, through long experience and collective memory, the strength of the hard Norwegian rock, its toughness, its fracture behaviour, its abrassivity and its ability to host high volumes of water under pressure in cracks and fissures. In this regard, Bane NOR insisted on several specifications for the TBM design (Table 2) and during procurement, insisted that:
• the proposed main bearing be increased in diameter
• reserves of power would be inbuild and assured and
• the machine would carry fixed drilling equipment able to probe ahead as well as drill pre-grouting injection arrays around the full 360 degree profile of the TBM drives.
These were extra costs that the client imposed on the bottom line of TBM procurement orders.
Lastly, the client included in the EPC contracts the procurement and installation of all fixtures and fittings including tracks, power gantries, signalling, communication and other mechanical and electrical systems. There would be no interface or hand over between different contractors for civil and M&E works. The one procurement contract would be responsible for all. The only handover would be to the client, Bane NOR, for the commissioning of the new trains and to take over service operations.
Let the works begin
The first civil works contract, for drill+blast and drill+split excavation of the 1.3km tunnels through the Ekebergåsen Hill, was awarded in February 2015 to Condotte of Italy. The contract included excavating a new alignment tunnel for the current and capacity-limited Østfold Line rail connection with Sweden and Continental Europe. Condotte was also awarded the adjoining EPC contract to bring all tracks approaching Oslo Central Station into a 625m cut-andcover alignment under Oslo’s famous Mediaeval Park and over the top of other urban underground infrastructure. Together the contracts at award totalled more than NKr3.2 billion (€300 million and US$325 million).
Table 2. TBM design specifications in tender documents
Hard-rock double-shield TBM
Core, probing and pre-grouting drilling systems
Mapping of probe holes by televiewer
Retractable cutterhead
Back-loading cutters
Cutter monitoring system
Minimum main bearing LIO life of 15,000hrs in compliance with ITAtech guidelines
Fully automatic guidance system
Automated electronic data recording system transmitting to main base in real time
Gas detection system
12 bar water pressure resistance in static mode
Grouting ports - number to be compliant with needs
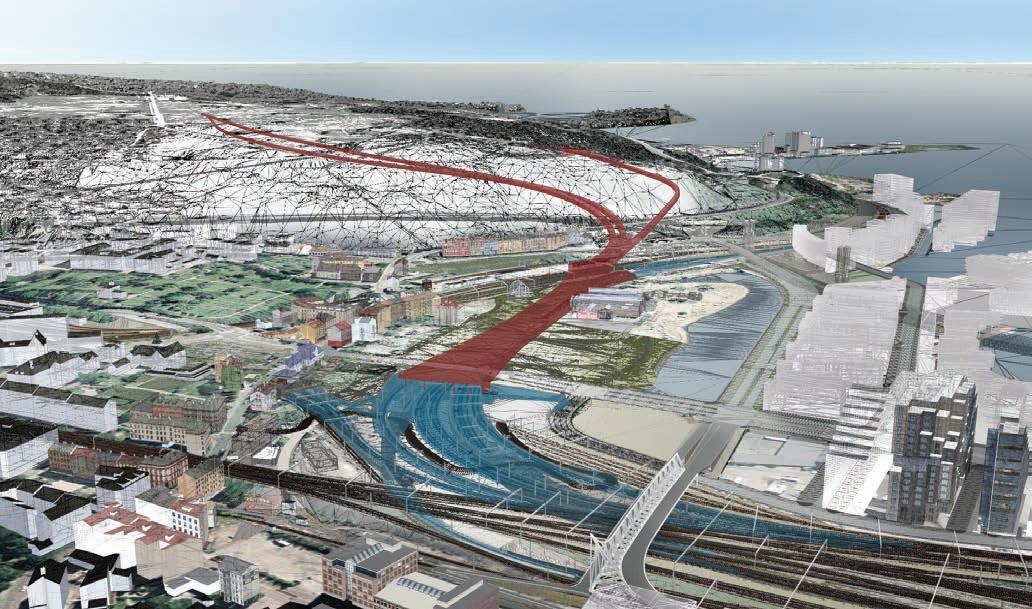
Drilling rigs - number to be compliant with needs
Non-flammable conveyor belts
Refuge chambers in compliance with ITA guidelines24hr stand-up time
TunnelTalk Archive – a chronology of the project
• International bid for Norway rail project - Dec 2008
• Direct twin-tube route for Oslo-Ski railway - Oct 2010
• Outreach for Norway's major rail tunnel project - Mar 2011
• Norway moves ahead with high speed rail - Oct 2011
• TBMs will excavate the Oslo-Ski Follo Line - Nov 2012
• Prequalification call for Oslo-Ski TBM link - May 2013
• Prequalifiers confirmed for Oslo-Ski Follo Line - Oct 2013
• Bids called for Oslo-Ski TBM drives in Norway - May 2014
• Acciona/Ghella selected for Norway TBM tunnel - Mar 2015
• Follo Line first tunnel contract award - Feb 2015
• Drill+split first for Norway’s Oslo-Ski Follo Line - Oct 2015
• Double shield TBMs take on Norwegian hard rock - Oct 2015
• VIDEO: Factory acceptance of Follo Line TBM - Jun 2016
• TBM tunnelling begins on Norway’s Follo Line - Sep 2016
• Race towards breakthrough in Oslo - Sep 2018
• Simultaneous breakthrough for Follo Line - Sep 2018
• All TBM boring complete for Follo Line - Feb 2019
• Pregrouting with double shield TBMs - Jul 2021
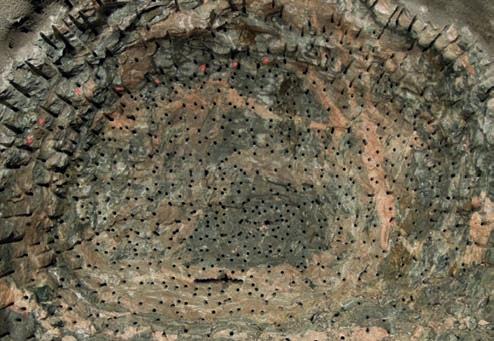
The third of the five large EPC main construction contracts, for expansive restructuring of infrastructure at Oslo Central Station was awarded in February 2015 to JBT Rive reetablere of Norway. In July 2015 construction of a new station and approach surface tracks for the Follo Line at the town of Ski and was awarded as a NKr 2.5 billion (€290 million) EPC contract to OHL of Spain.
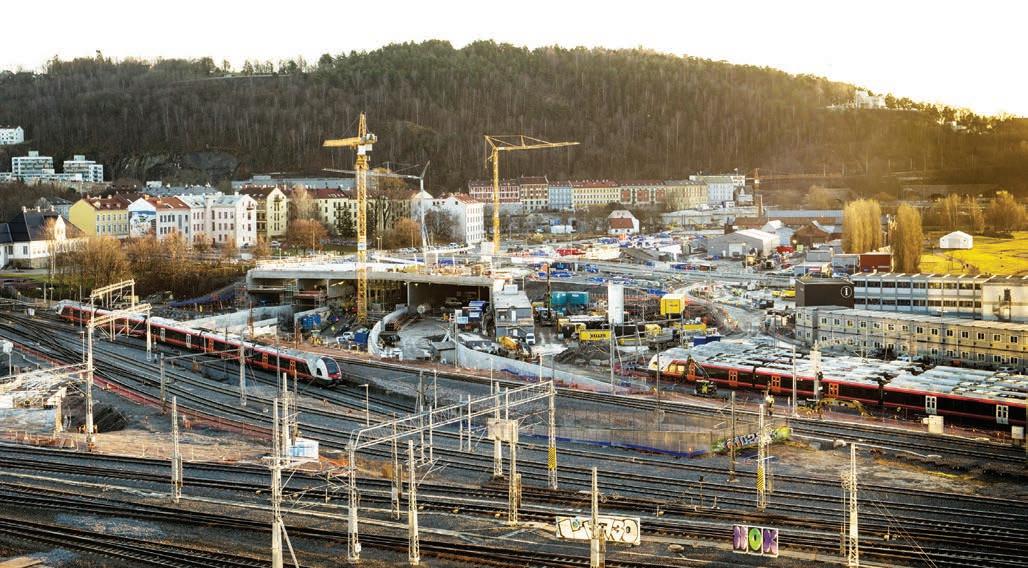
Design and construction of the Ekebergåsen headings through the Precambrian gneiss rock with deposits of
alum shale faced particular concerns due to the presence of existing underground infrastructure including raw water tunnels and sensitive watertight oil storage caverns. In areas of close proximity to these underground structures, the less disruptive method of drill+split had to be engaged.
At Oslo Central Station, the 625m of cut-and-cover works had to bring three trackways - one for the new Østfold inbound track and two for the new Follo Line - to allow arrival of trains at underground station platforms. The cut-andcover area was characterised by severe and well-known quick clay geotechnical conditions of the inner-city area near the shores of the Oslo fjord. These required extensive use of jet grouting improvement for controlled excavation.
The fifth and largest contract for the now named Blix TBM tunnel was awarded in March 2015 to the Spanish/Italian JV Acciona/Ghella. This contract represented the largest ever onshore civil engineering contract in Norway. The specifications for the deliverables were high, as was the responsibilities for work progress and delivery across time.
Using the specified four double-shield TBMs from one central access site, the JV was committed to completing the EPC contract at its contract award price of NKr 8.7 billion, about US$1.2 billion in 2015 conversion rates and meet a minimum design life of 100 years.
One of the first challenges for the project was bankruptcy of the Italian firm Condotte on the Ekebergåsen and Oslo Station approach tunnels. The situation was addressed head on by Bane NOR with termination of the contracts in 2018 and award of the works in four, rather than two, new contracts. With the restructure behind them, work progressed and the months of time lost was made up to the point of limiting the impact to an overall project and the cost impact to about NKr 2 billion.
Across all elements of construction, the project accumulated a delay of one year and a increase in cost of about NKr 11 billion. Set in 2014, the project in all its various parts was to be in operation in December 2021 and at a 2014
Government budgeted cost of NKr 26 billion (about €2.48 billion and US$2.64 billion in current exchange rates). At the opening of the new infrastructure in December 2022, the time has extended by a year and total project cost at turnout is reported at NKr 36.8 billion (about €3.55 billion and US$3.77 billion in December 2022 exchange rates), a cost increase of about 40% across eight years.
For the project as a whole, the 20km twin tube Blix tunnel contract was the critical path element. At an award price of NKr 8.7 billion (about US$1.2 billion at the time), it was by far the largest of the project contracts and would require close cooperation and management by both Bane NOR and the Acciona/Ghella JV. Under Acciona/Ghella Project Directors Fernando Vara and Giovanni Giacomin respectively, the JV mobilised efficiently at the central rig area jobsite and had the demands of the project under control. Both JV Project Directors brought extensive project management and TBM excavation experience to the project. Vara had worked on
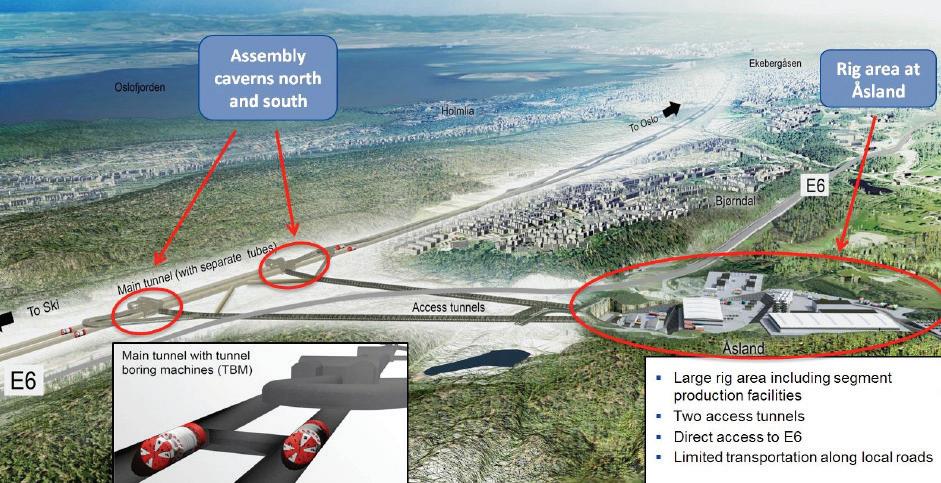
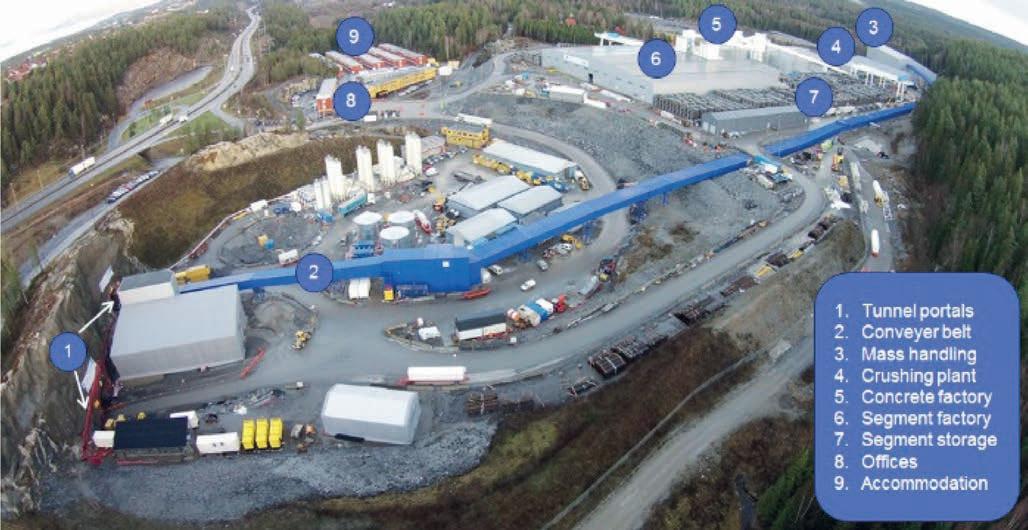
the famous Guadarrama TBM railway tunnel project in Spain and Giacomin had worked on the Kárahnjúkar TBM hydro tunnel in Iceland in the early 2000s and had just finished managing the Legacy Way TBM highway link project, in joint venture with Acciona and an Australian partner, in Brisbane, Australia. Project Manager for the TBM excavation works at the Follo Line, Matteo Ortu of Ghella, was also a construction manager on the Legacy Way project.
Along with the two 1km long access adits, the large central rig area jobsite houses the onsite segment precast factory, the muck handling stockpiles and wastewater management ponds, as well as dormitories for the workers, management offices, materials laboratories, workshops and importantly,
a big canteen and cooking facilities for feeding the more than 1,000 workers engaged on the contract at its peak.
To get works started, AF Gruppen of Norway was subcontracted to excavate the two 1km long drill+blast access adits and TBM assembly and working chambers at the junction with the twin tunnel alignment. At the same time construction of the precast segmental lining factory got underway and an order for all four TBMs was placed with Herrenknecht.
The four 10m diameter double-shield TBMs were all manufactured at the Herrenknecht Schwanau factory in Germany, with the first dispatched for delivery by road
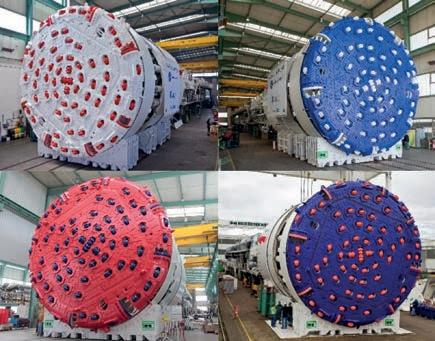
From left: After contract signing by Fernando Vara and Giovanni Giacomin for Acciona/Ghella JV and Anne-Katherine Kalager of Bane NOR (front, with colleagues), the JV ordered four 10m diameter double shield hard rock TBMs manufactured by Herrenknecht in Schwanau, Germany. Know more about the design and manufacture of the TBMs in the videos

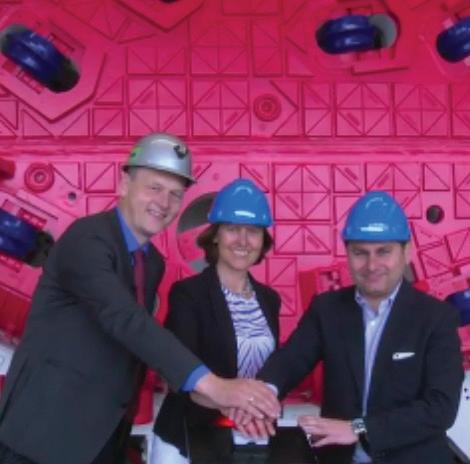
Table 3. Design details of the four Herrenknecht double-shield
TBM cutting diameter 9,960mm with new cutters
Cutter size 19in wedge lock, back-loading
Number of disc cutters 4 Centre (x 2 discs) + 48 face+ 15 gauge equals 71 cutting discs
Load per cutter ring 315kN
Max recommended cutterhead load 71 x 315 = 22,365kN

Weight of cutterhead 265 metric tonne equipped with cutters
Cutter monitoring system Five cutter positions monitored (42, 44, 46 48, 50)
Cutterhead power 13 each VFD motors x 350kW = 4,550kW
Total power installed Approx 6,900kW
Cutterhead rotation 0 - 6.06 rev/min
Nominal torque 11,115kNm at 3.67 rev/min
Max overload torque 16,672kNm at 3.67 rev/min
Main bearing Three axis roller bearing, 6,600mm o.d. for a bearing TBM diameter ratio of 0.66
Main bearing life Greater than 20,000 hours according to ITAtech guidelines
Main bearings seals
Inner and outer ceiling system, each: 3 lip seals + activatable seal ring for 12 bar static water pressure resistance
Total length: TBM and back up About 150m
Total shield length 14.4m
Total weight: TBM and back up About 2,300 metric tonne
Drilling equipment and abilities Two drill rigs with rod adding system for drilling up to 44m long holes for probing and pre-grouting through 38 ports in the gripper shield with 11 degree angle to tunnel and through 8 openings in the cutterhead
FOLLO LINE, NORWAY
A THOUSAND TONNES OF INGENUITY
Four Double Shield TBMs running in parallel, rock strengths of up to 268 MPa, and managing potential water pressures of up to 12 bar – Follo Line is undoubtedly a technical and logistical top-class project. Smart engineering, unshakeable willpower and mutual trust between all partners are necessary to make Norway’s biggest infrastructure project a success. Final double-breakthrough in February 2019. herrenknecht.com/hardrock

to Norway in early 2016 and the last in July 2016. In their design, the 10m diameter TBMs, with their larger 6.6m o.d. bearings, mounted drill rigs and 19in disc cutters, are designed to face and overcome all that the hard Norwegian rock can present, including strengths of up to of up to 300MPa in UCS and potential high volume, high pressure water ingress (Table 3).
By the end of 2016, all four TBMs were underway working in opposite directions from the central working site at Åsland. Very soon the steady routine of segmentally lined excavation
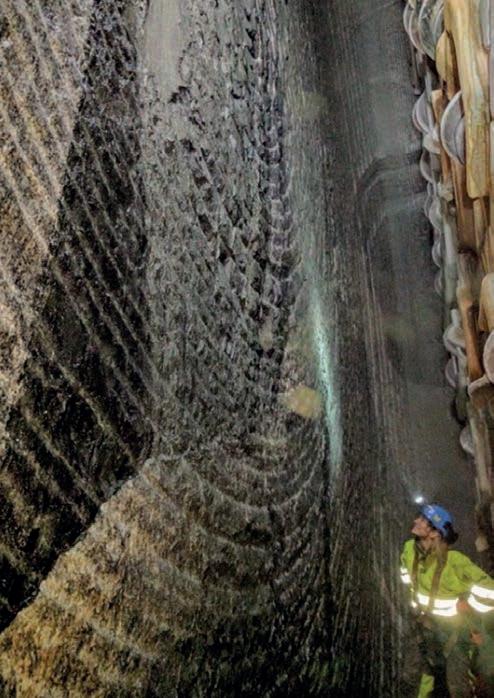
on a 7 days/week, 24 hours/day schedule, was established and reaching averages of 15m/day per machine and recording a best day of 36m and an accumulative progress best of 2km/month by all four machines (Table 4). This was supported by the continuous conveyor systems supplied by MartiTechnik removing tonnes of excavated rock per day, the MSV rubber tire multi service vehicles supplied by TMS that carried segments and men and materials to and from the TBMs as they progressed, and by operation of the double shield grippers that allowed simultaneous TBM excavation and precast lining ring build. A visit to the job site hosted by the Acciona/Ghella JV as part of the World Tunnel Congress held in Oslo in May 2017, confirmed that the TBMs operated most of the time in double-shield mode, only rarely having to apply forward thrust off the segmental lining. Behind the segments, the annular gap was backfilled with a two component grout, rather than the more usual pea gravel and mortar in segmentally lined rock TBM tunnels, with both parts pumped from the surface to holdling tanks on the TBM backups.
The precast segmental lining comprises seven segments and a key in each 400mm thick x 1.8m wide x 9.55m o.d. (8.750m i.d.) ring plus an invert-infill element to create the rail bed. The segments are reinforced with rebar cages and fitted with cast-in sealing gaskets. More than 140,000 segments and 20,000 invert infills were produced in the on-site production factory that went on to produce other required precast elements. The on-site batching plant produced the concrete required for element casting and cast in place concrete needs and on-site facilities also produced all the mortar and grout needed for pre-excavation grout injection and secondary contact grouting. The moulds, carousels and lifting hoists for segment fabrication were supplied by the cbe Group of France, with the cast-in sealing gaskets supplied by Sealable and installed into the moulds before the rebar reinforcement cages were installed and concrete poured. The greatest interruption to the established double-shield boring-lining routine was the TBM stoppages to deal with
Max daily excavation 28.8m 34.2m 36m 32.4m
Max weekly excavation 149.3m 162m 160.18m 141.3m
Max monthly excavation 523.2m 583m 490.8m 518.31m
Pre-grouting excavated - 7.637km 1,448m 1,350m 2,197m 2,641m
water ingress. At times, as much as 80 litre/min was recorded pouring through a single 44m long probe hole. A volume of 15-40 litre/min from one to four probe holes, in less sensitive areas, and 5-12 litre/min from probe holes in highly sensitive areas triggered a pre-excavation drilling and grout injection cycle to reduce the water inflows back to specified limits.
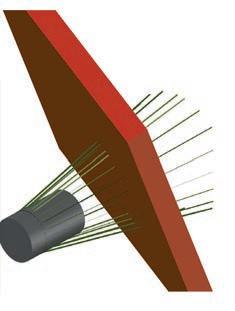
In zones of particularly high water ingress, more than 100% of work time/week was consumed by drilling patterns of 38 x 44m long grout holes in the 360˚ overlapping arrays and completing the programme of grout injection.
In the contract, Bane NOR had estimated that about 1,600m in total, or some 4.4% of total 36km of bored tunnel by the four TBMs, would required pre-excavation grouting. At breakthrough of the last of the TBMs, the total length of pre-excavation grouting was 8,000m or some 22.22% of the total bored length.
With the increased need for pre-grouting, the trigger values, drilling needs, equipment and processes involved in each cycle was revised, improved, and upgraded as the TBM headings progressed. Some of these improvements

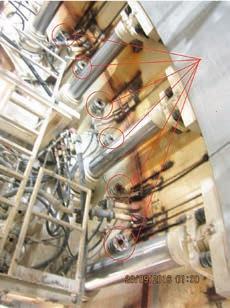
included simultaneous hole drilling and grout injection activities and installing fixed grout pumping equipment on the TBM backups rather than using mobile grouting units.
With four TBMs progressing simultaneously and all systems operating like a well-oiled machine, the meters of hard rock were chewed up at a combined rate of more than 2km/month (Table 4). Some 36km of 10m diameter double-shield segmentally lined TBM excavation was completed within 30 months. After launch of the first machine in September 2016, the two TBMs heading to Oslo completed a double TBM breakthrough into a chamber at the start of the drill+blast alignment of the neighbouring Ekeberg tunnel in September 2018. Following launch in November and December 2016, the final two machines achieved their double-TBM breakthrough in February 2019 into the transition portal to the surface approach to the new station in Ski.
While the achievement of the TBMs was a major milestone for the project and all who contributed to the success, it was just the beginning for Acciona/Ghella of the installation works
In February 2019 the last two TBMs completed a simultaneous breakthrough at the transition portal to the surface approach to the new station in Ski, marking the end of 36km of TBM segmentally lined bored tunnel within 30 months and following double breakthrough of the first two machines into underground caverns at the start of the drill+blast tunnels near Oslo in September 2018
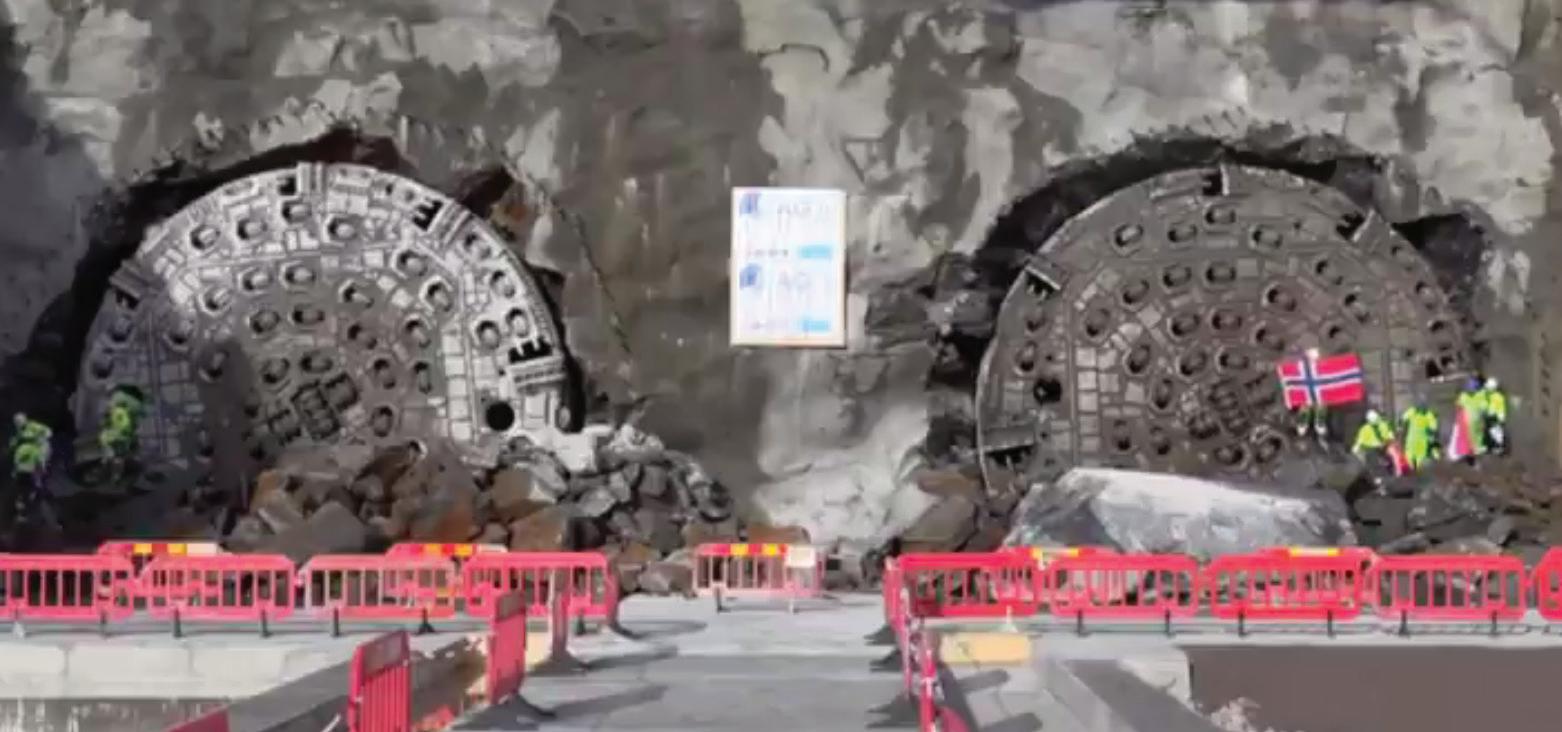
Haulage by MartiTechnik continuous conveyors
To manage the muck haulage, Acciona/Ghella JV commissioned MartiTechnik of Switzerland to produce, deliver and supervise the assembly of a complete continuous conveyor belt system. The system was a complete package to convey muck from behind the TBMs excavating the four headings of the twin tube running tunnels and transport the muck through the 1km access adit and across the large rig area job site to the different dumpsite stockpiles.
At full length this complete order comprised more than 40km of belt conveyor.
The four TBM conveyors off-load onto a set of 12

One of the two access adits was dedicated to the two main conveyors from the TBMs to the surface

MartiTechnik AG
Lochackerweg 2 CH-3302 Moosseedorf Switzerland
Tel: +41 31 858 33 88
Email: info@martitechnik.com Web address: martitechnik.com
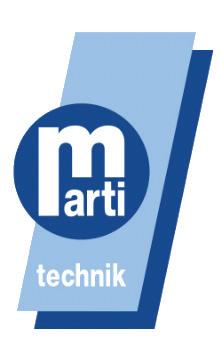
conveyors that make up the two 1.9km long conveyors that move muck up through the drill+blast access adit and feed different stockpiles. Drive power for the conveyor sets was 8,716kW.
The order for MartiTechnik was a vote of confidence in the company’s ability to fulfil delivery of a system of this scale and complexity and keep it running with the minimum of downtime to keep the project on schedule.
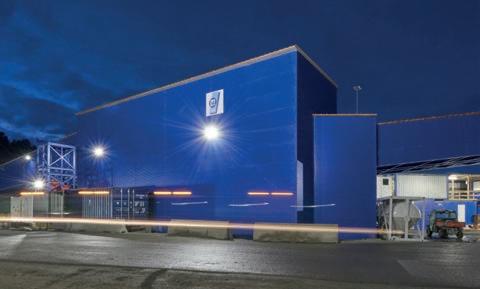
Drive tower for the dumpsite conveyor
TBM supplies assured
For managing services behind the advancing TBMs of the project, the Acciona/Ghella JV procured a fleet of seven multi-service vehicles (MSVs) from TMS of France.
Driven electrically, or by diesel or alternative fuels, and running on either pneumatic or solid rubber wheels, the MSVs travel on the invert of the segmentally lined headings as easily as on the roadways of the access adits and the job site. In Norway, MSVs ferried workers at crew changes to and from the four TBMs and kept a constant delivery of segments and materials to the machines, each segment vehicle carrying two invert infills and 14 segments of two rings on each trip.
A main advantage of MSVs is their mobility even on the steep fully loaded decline of the 1km long access adits from the surface to the underground rail alignment of the Follo Line drives. With independent axle suspensions, the wheels of the vehicles are always in full contact with the ground with the steering function of the rear wheels allowing navigation of tight radius curves. This was a priority requirement at the bottom of the access adits on the Follo Line and into the four TBM headings.
As part of the Herrenknecht Group since 2012, TMS has been leader in the development of the rubber tired multi-service vehicles with the driver unit at both ends of the unit that prevents reversing or turning the vehicles around, ensuring enhanced safety and efficiency in TBM headings.
Segments for two rings per MSV taking a tight turn into a Follo Line TBM heading
24, ZI Rhône Vallée Sud 07250 Le Pouzin France
Tel: +33 475 85 85 30 Email: info@tms-company.com Web address: tms-company.com
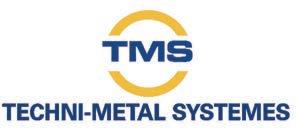
SEALABLE the watertight gasket solution
The challenge for the segmental lining of the Follo Line project in Norway was the the particularly hard rock, the prospect of high-volume water inflows at high pressure, and a tight project management specifications and production requirements for all applied systems, materials and supplies. As an example, three production lines running in parallel were required to fabricate the lining segments for the four TBM headings of the Blix tunnel. There were also strict environmental regulations protecting the natural water table of the host rock. To meet these concerns, the contractor selected SEALABLE to supply the gaskets for the segmental lining and to choose a cast-in anchored gasket as opposed to a bonded seal.
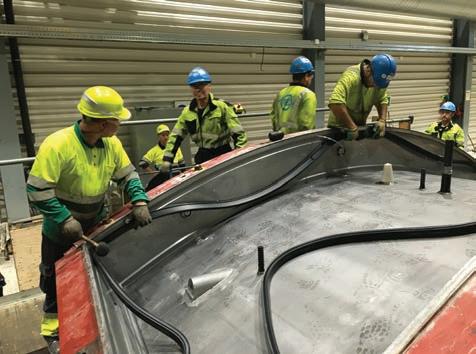
The sealing solution delivered to the project was created specifically by SEALABLE. The gaskets were tested in its own technical centre and then tested again at STUVA, the construction materials research laboratory of Germany.
The required tightness of 33 bar was proven to a safety factor of two.
The main accreditation of the project for SEALABLE has been:
• An accelerated manufacturing process to meet the high segment production demand
• Accuracy of the gasket fit through and adaptation of the sealing gasket corners
• A specific consideration for its products to be environmentally friendly
• The certified STUVA leak proof testing
SEALABLE Solutions GmbH
Eisenacher Landstraße 70 99880 Waltershausen Germany
Tel: +1 732 763 6203 Tel: +49 (3622) 633-0 Email: info@seal-able.com Web address: Seal-able.com
High production segment fabrication
For the cbe Group of France, its delivery of 144 moulds, three steam-curing carousels and three pre-storage carousels to the Follo Line project was a first for the business and its largest order to a single precasting site.
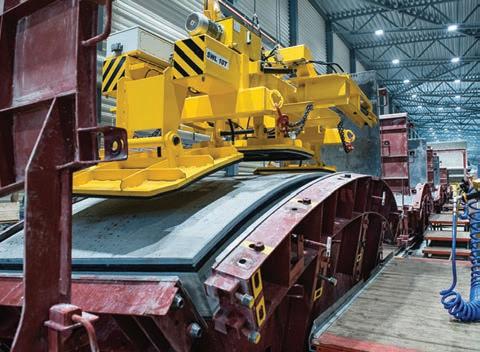
The 144 moulds provided for production of a total 18 rings on each of the three production carousels simultaneously. The special pre-storage carousels, one each for the three production lines, allowed the segments to cool gradually before moving them to the stockpiles outside. This avoided any thermal shock between the high temperatures of the curing chamber and the cold temperature of a Norwegian winter outside. The cooling down process has a great impact on the quality of the concrete.
The cold climate was also an important element in the conception of the outdoor lifting tools such as the outside stockpile storage clamp and the external
cbe Group

17 rue F Joliot Curie
37550 Saint Avertin France
Tel: +33 247 37 53 64
Email: cbe@cbegroup.fr
Web address: cbe-tunnels.com
segment transport trolley. The latter was customized especially for this project, using for the first time the induction alimentation system, developed by cbe Group company Acimex.
ACIMEX
26 rue Paul Langevin
37550 Saint-Avertin France
Tel: (+33)2 47 25 57 85
Email: contact@acimex.net
Web address: acimex.net
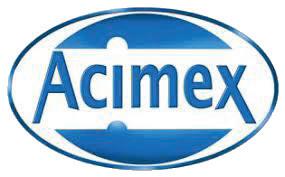
of all the M&E equipment and systems. More than 36km of track had to be laid, all power cables on catenaries had to be installed and all the support systems and equipment, including in-tunnel jet fans for longitudinal ventilation during rail operations and the continuous evacuation walk-way along the tubes and the cross-passages between the two running tunnels had to be completed.
By October 2022, the joint venture met its EPC target and handed over a ready-to-use railway system in the underground environment of the longest rail tunnel in northern Europe. The achievement, despite the challenges, is a credit to Bane NOR as the client and all who contributed to the effort.
Now in operation, the new Follo Line allows the rail capacity in the south corridor from Oslo Central Station to increase from about twelve to forty trains per hour with local and freight trains using the realigned Østfold Line and regional and express trains using the new Follo Line infrastructure. This increased rail capacity for southern Norway is expected to support 11,000 more public transport trips through the corridor per day, represented by a 67% increase during rush-hours and 43% at off-peak times. This allows a reduction of 5,800 car trips per day on the local roads and reduces carbon dioxide emissions by an estimated 5,474 tonne per year. Together with better passenger connections and the start of high-speed rail services to Sweden and Europe beyond, the Norwegian
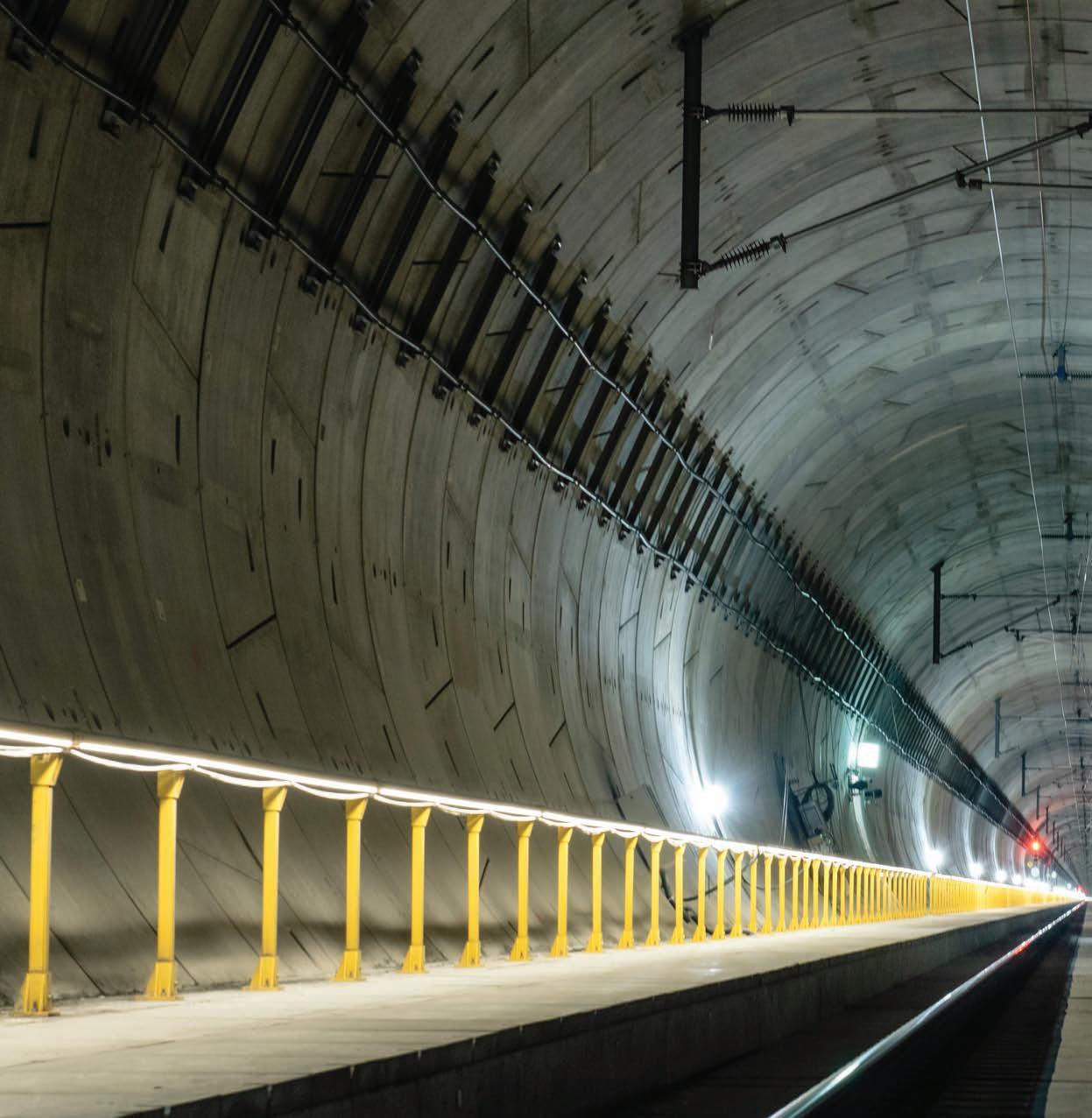
Together with the TunnelTalk reporting through the years, NFF, the Norwegian Tunnelling Society produced an indepth publication about the tunnelling experience for the Follo Line project.
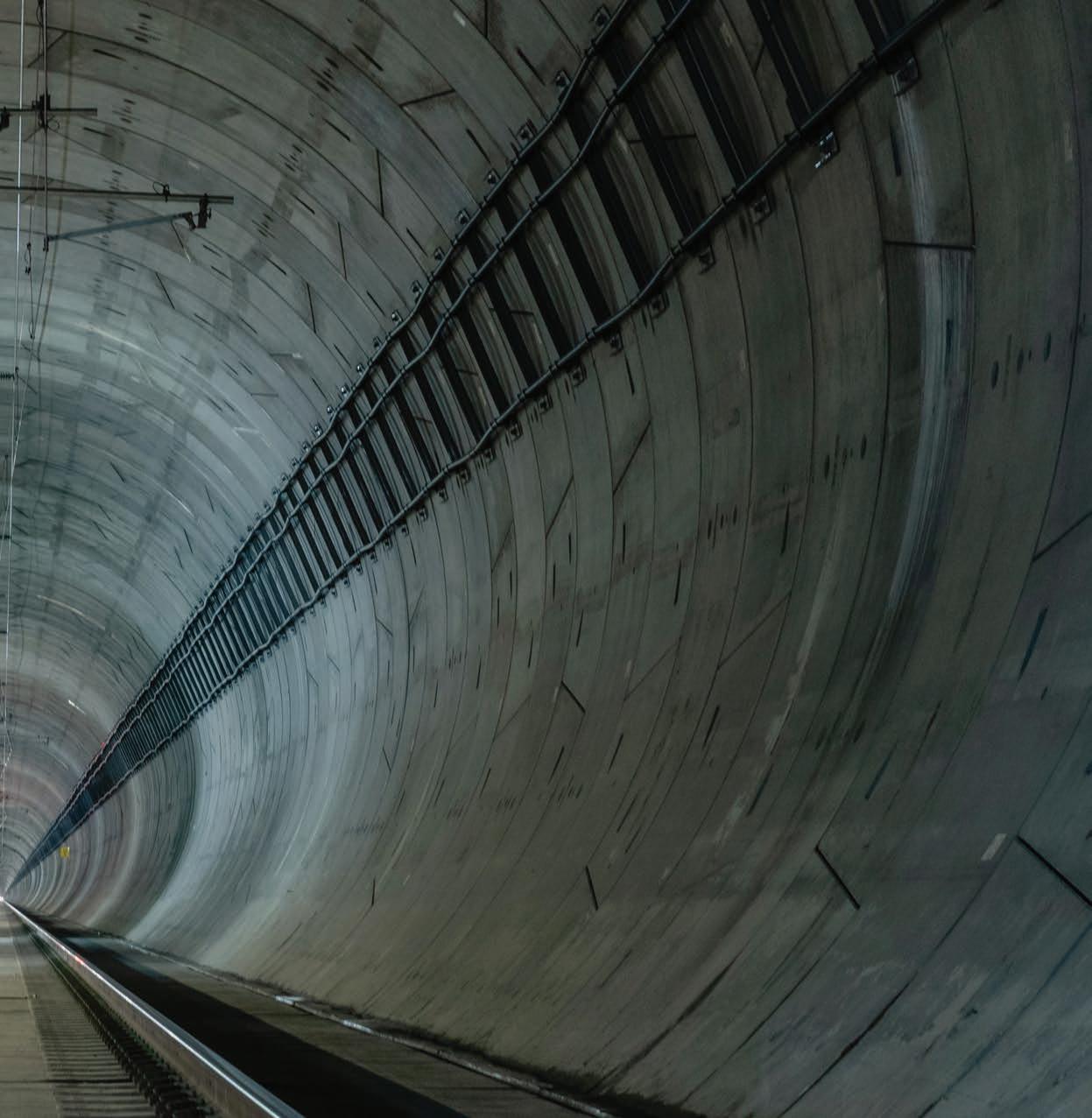
Download a pdf copy of Publication No 29 from the NFF website.
Government has also set a goal of tripling the amount of rail freight on the Østfold Line by 2040. For the south corridor this equals removal of 750 trucks per day from European Route E18. These are significant developments and forward-planning investments by Norway into its future, its closer integration with mainland Europe and for the world in which future Norwegian generations will live. n
TunnelTalk references
• Spain rock TBM marathon at Guadarrama - Nov 2005
• 60km of TBM tunnelling complete at Kárahnjúkar, Iceland - April 2008
• Celebrating success at Legacy Way in Brisbane - Dec 2013
• Breakthrough on Uleiken inspires TBM excavation in Norway - Jan 2018
• Surface challenges for underground solutions - Feb 2019
• Rock-solid tunnelling by Follo Line TBMs - Oct 2018
• Tailor-made TBMs for Norwegian hard rock - Feb 2019
• Pregrouting combined with double shield TBMs - Jul 2021